bigredinohio
Member
I sanded the 1708 this morning with my disk sander and feathered the edges with my finish sander before the rain.
Then I pushed back into the garage for layer #2.
These were full when I started and here is what I went through in two days for two layers of 1708 on the transom.
Two thumbs up from the daughter makes it all worth while!
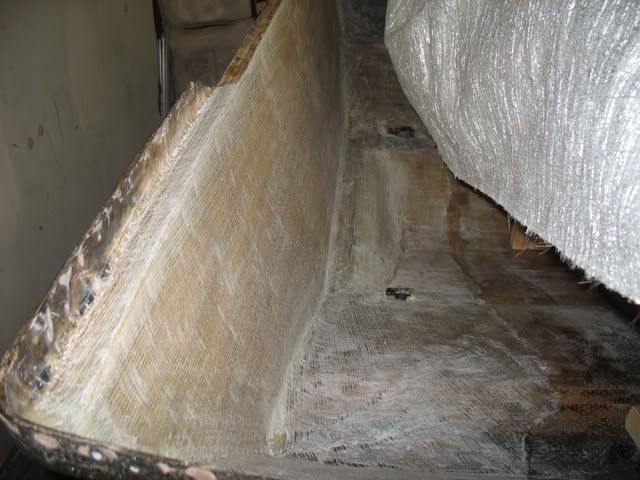
Then I pushed back into the garage for layer #2.
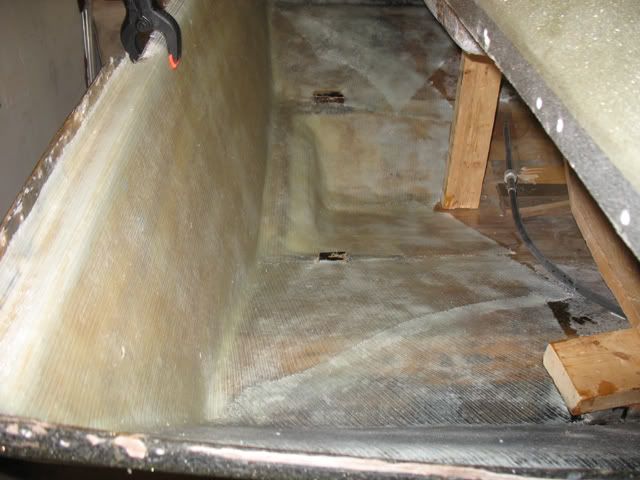
These were full when I started and here is what I went through in two days for two layers of 1708 on the transom.
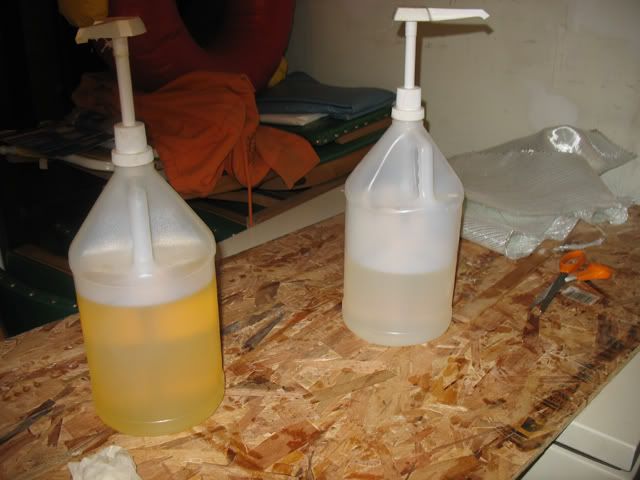
Two thumbs up from the daughter makes it all worth while!
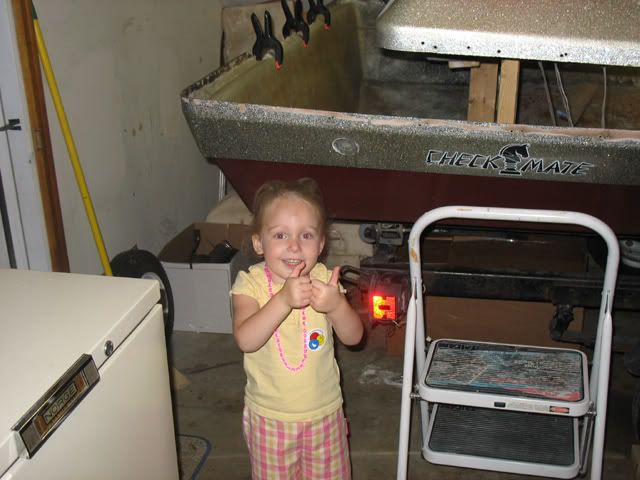